Les Papeteries Latune
I – L’eau
Il – Le chiffon
III – La fabrication du papier
La pâte de bois
Les raffineuses
La machine à papier
IV – La production de la vapeur
VI – La salle de triage
Le laminoir
Les cartes de visite
Les cartes de deuil
VII – Services administratifs et expéditions
L’expédition
VIII – La vie sociale
La petite école
Les fêtes de Noël et de Pâques
L’éducation des jeunes filles
Les logements
Les jardins
La coopérative
Les loisirs
La santé
Fonctionnement et vie de l’entreprise
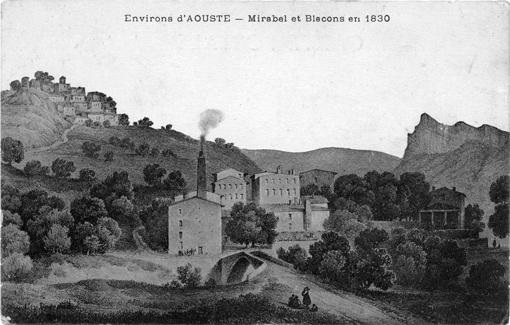
I – L’EAU
Comme le faisaient MM. Latune, lorsqu’ils faisaient visiter leur usine, la visite commençait par le haut, où arrive le canal. Aussi nous commencerons nos témoignages de la même façon.
L’eau a un rôle essentiel pour l’implantation de la fabrique.
Utilisée pour la fabrication du papier et comme force motrice, d’où la disposition judicieuse des bâtiments, établis en gradins au flanc d’un coteau, ce qui permettait l’utilisation de l’eau par gravité.
Le canal d’amenée d’eau est toujours en fonctionnement, puisqu’il est utilisé actuellement pour fabriquer de l’électricité. Sa prise d’eau sur la rivière Gervanne, au dessus du hameau des Berthalais, est à environ 2500 mètres de l’usine. L’eau de la Gervanne, à l’époque où l’on fabriquait le papier, était réputée pour sa pureté et c’est cette qualité de l’eau qui contribuait à la renommée du papier de Blacons, et pour preuve, la plupart des riverains du canal l’utiliseront comme eau potable jusqu’à la mise en place du réseau communal en 1962.
Au-dessous de l’arrivée du canal, à une dizaine de mètres en contrebas, s’étendait un bassin de terre d’environ 120 m de long, 12 m de large, 2 ni de profondeur et un autre plus petit de 90 m2 environ, plus profond, et qui se trouvait à la suite du grand, devant le mur Est du bâtiment des raffineuses. Ces bassins constituaient une réserve d’eau claire lorsque la rivière, et par conséquence le canal, étaient troublés par les pluies.
A l’emplacement de ce bassin se trouve à ce jour le mini-golf. Sous le bâtiment le plus au nord, au-dessus des bassins, deux citernes voûtées recevaient une réserve d’eau de 500 m3 environ. Ces réserves d’eau claire permettaient à l’usine de continuer sa fabrication, en attendant que l’eau du canal se décante.
Au dessous du grand bassin, les jardins réservés au personnel de l’usine étaient arrosés par l’eau de celui-ci. Aujourd’hui le terrain de sport occupe cet emplacement.
Une partie de l’eau du canai était conduite dans un local appelé salle des filtres, qui avait été conçue par M. Berger, ingénieur-papetier et associé de M. Charles Latune. Dans cette salle, l’eau cheminait dans des caniveaux vers de petits bassins en maçonnerie, où étaient placées transversalement des grilles en toile de cuivre, montées sur des cadres en bois, dont la fonction était de filtrer l’eau circulant lentement dans les bassins. L’eau filtrée, partait par gravité, au moyen de conduites en cuivre, vers la fabrication du papier.
L’autre partie de l’eau servait de force motrice, au moyen de turbines qui actionnaient directement les machines par la seule force hydraulique, sauf une, qui produisait de l’électricité, mais seulement lorsqu’il y avait assez d’eau dans le canal.
Il y avait au total six turbines. Une première actionnait les défileuses, les lessiveuses et le blanchiment. Une deuxième pour les raffineuses nord. La troisième fabriquait de l’électricité. Une quatrième faisait marcher les raffineuses sud et le meuleton. La cinquième mettait en mouvement la calandre. La sixième faisait fonctionner la machine à papier.
Mais en été, pendant la période de sécheresse, une machine à vapeur genre locomobile, de marque « Pinguély », célèbre dans le village pour son grondement de locomotive, suppléait au manque d’eau, en actionnant les raffineuses nord.
Les propriétaires de la Papeterie n’avaient pas négligé le côté esthétique. Devant la place de l’actuelle Mairie, un jardin en creux, rempli d’arbustes et de verdure, traversé par un petit ruisseau et agrémenté d’un jet d’eau, égayait les bâtiments austères disposés tout autour.
La rivière Drôme était utilisée. Une turbine était installée à 150 mètres environ en aval du pont sur la Drôme. Le local de la turbine a été agrandi et aménagé par Mme Jean Latune, veuve du dernier propriétaire de la Papeterie, et elle l’occupe actuellement comme résidence secondaire. Cette turbine servait uniquement à fabriquer de l’électricité. Toute la production d’électricité était en 500 volts.
L’eau d’alimentation de la turbine arrivait par un canal dont la prise d’eau se situait sous le Pont de Nodon sur la D93 vers Saillans. La vanne et l’ouvrage en maçonnerie sont encore en place à ce jour.
Le canal de 1700 m débouchait sur un bassin construit en s’évasant, avec un déversoir dans un caniveau annexe. Au fond du bassin, une grille filtrait l’eau, qui était ensuite turbinée et rejetée dans la Drôme. Ce bassin, qui comprend toutes les parties maçonnées, avait 25 m de long, de 5,80 m à 2,80 m de large et 2,50 à 1,20 m de profondeur.
Il a fait longtemps, c’est-à-dire jusqu’en 1972, la joie des baigneurs, car avec ses parois cimentées, son eau calme, sa profondeur, la natation et le plongeon étaient favorisées. Aussi un bon nombre de Mirabélais (habitants de Mirabel) et les habitants des communes voisines – y compris Crest – ont appris à nager et à plonger grâce à ce bassin. Les propriétaires de la Papeterie ont toujours montré beaucoup d’indulgence et de compréhension envers les baigneurs, qui quelquefois, cassaient les vitres du local ou ornaient d’inscriptions le crépi du bâtiment.
Le nettoyage des deux canaux s’effectuait autrefois la semaine de l’Ascension, ensuite à la fin des vacances, fin août. C’était le personnel masculin de la fabrication qui était chargé de ce travail. Le curage se faisait à la pelle, la végétation était taillée par les « bousquatiers ». Le travail était pénible. Un remontant était nécessaire, quelquefois consommé généreusement, ce qui laissait de bons souvenirs…
II – LE CHIFFON
C’était la matière première utilisée depuis la création de l’usine, jusqu’en 1955 environ. Mais les dernières années, il était peu utilisé sauf pour le buvard, qui n’était fabriqué qu’avec du chiffon et en mélange avec la pâte de bois, pour certains vélins de qualité supérieurs. Le chiffon provenait de plusieurs endroits mais en particulier de la région de Marseille. Il était acheminé par chemin de fer, puis repris de la gare par des voitures à cheval, ensuite par des camions automobiles.
Au XIXe siècle, avant le passage de la ligne Livron-Aspres, le voiturier de la Papeterie allait chercher le chiffon à Livron, ensuite après la mise en place de la voie ferrée, il n’allait qu’à Aouste-sur-Sye. Les balles de chiffon enveloppées de jute, pesaient environ 200 Kg. Ces balles étaient stockées dans le bâtiment du haut de l’usine, celui qui comportait des citernes à eau au sous-sol. De là, transporté par un chariot, le chiffon était acheminé vers la batteuse. Les chiffons déballés était introduits dans cette machine qui les dépoussiérait. Cette poussière, évacuée par une ouverture à ciel ouvert, se répandait sur le sol, mais aussi sur les arbres et arbustes des alentours. Cette batteuse mue mécaniquement ressemblait à un grand vannoir à grains. A la sortie de la batteuse, le chiffon était déposé sur une grille, deux ouvrières se faisant face enlevaient le « fraisun », c’est-à-dire : le papier, les morceaux de bois, le fil de fer etc… tout ce qui n’était pas du chiffon.
Ainsi trié, le chiffon était stocké au même niveau, ou bien chargé dans de grands carrés de toile de jute appelés « chairriers « , il était monté à I’ aide d’un palan à corde au 1er ou au 2ème étage du bâtiment. De ce stockage, ou directement après le dépoussiérage-triage, un ouvrier approvisionnait les coupeuses-trieuses de chiffon. Ces ouvrières assises sur tabouret de bois, avaient devant elles une table grillagée, au centre de laquelle était fixée par des coins de bois, une lame de faux au fil très coupant. Disposés en demi cercle autour de la table, des sacs de juste cerclés de fer à l’ouverture et maintenus rigides par des fils de fer fixés aux chevrons de la charpente, recevaient le chiffon coupé et trié. L’ouvrière enlevait les ourlets, les boutons, puis coupait le chiffon en grandes bandes d’environ 5 cm et réunissant ces bandes, elle les recoupait en morceaux de 15 cm environ. Ainsi coupé, elle jetait le chiffon dans les sacs, en prenant soin de le classer par catégorie : coton 1, coton 2, coton 3, ourlets, lin, chanvre.
Les trieuses étaient rémunérées au poids de chiffon coupé. Le responsable du chiffon pesait les sacs remplis et inscrivait sur un registre, le poids et la catégorie du chiffon.
Ensuite il vidait les sacs dans de grands casiers appelés « macalons » en respectant la catégorie triée (ces casiers ont été abandonnés dans les dernières années de production de chiffon). Des macalons, le chiffon transporté dans les chevriers était mis en dépôt au 1er et 2éme étage, monté avec le palan et rangé par catégorie. Au 1er étage au dessus du triage, le chiffon était passé dans une machine appelée « le Loup ». Cet appareil semblable à la batteuse, mais muni de dents d’où son surnom, effectuait un second dépoussiérage qui parachevait le travail dégrossi par la batteuse, mais agissant cette fois-ci sur le chiffon coupé. La transmission mécanique du loup avait un engrenage placé à l’extérieur du bâtiment et son grincement strident et monotone remplissait d’inquiétude les enfants que nous étions, ce bruit insolite renforçant encore le mystère du loup. A la sortie du loup, le chiffon était envoyé dans les lessiveuses, cylindres en acier rivé de 2,5 m de diamètre et de 3 m de long environ, d’une contenance approximative de 8000 l ; il y avait 2 lessiveuses. On introduisait environ 1000 kg de chiffon, en ajoutant de la chaux vive préalablement éteinte, de la soude caustique, de l’eau, de la vapeur. Le chiffon tournait de 8 à 12 heures dans la lessiveuse, qui tournait horizontalement sur deux paliers. Ensuite il était vidé à côté de l’appareil et transporté avec des corbeilles vers les défileuses. Etablies dans le bâtiment contigu aux lessiveuses, se trouvaient plusieurs défileuses. C’était une machine avec un bâti extérieur en fonte, l’intérieur était en maçonnerie avec des profils bien étudiés. Une platine en fer munie de dents, et fixée sous un rouleau mobile, équipé lui aussi de dents en fer, effectuait le défilage du chiffon.
Les corbeilles de chiffon lessivé étaient vidées dans l’appareil, l’eau coulait continuellement à l’intérieur ; il fallait prendre garde à ne pas trop mettre de chiffon, sinon le rouleau se bloquait. Lorsque le chiffon était bien travaillé, l’ouvrier ouvrait une vanne placée au fond de la défileuse et le chiffon déjà pâteux s’écoulait dans des conduites de cuivre, pour tomber dans les caisses situées à l’étage au-dessous.
Les caisses étaient construites en maçonnerie, le fond et les angles étaient revêtus de carreaux perforés pour permettre l’écoulement de l’eau contenue dans le chiffon pâteux. Cette pâte restait en dépôt dans ces bassins avant d’être emportée vers le blanchiment.
Prise dans les caisses, la pâte de chiffon était chargée dans un grand chariot sur rails, puis poussée et déversée dans le blanchiment qui se trouvait à quelques mètres de distance et à un niveau inférieur de 60 cm environ. Construits en maçonnerie, ces bassins de blanchiment au nombre de deux, étaient équipés pour l’un d’une hélice en bronze placée au fond, pour l’autre, d’une roue en cuivre avec des pales en bois. Leur rôle était de mélanger et de donner un mouvement à la pâte. On ajoutait à la pâte du chlore et de l’eau, la durée de malaxage était d’environ 4 heures, il fallait obtenir un produit blanchi. Pour vider les bassins, l’ouvrier ouvrait la vanne placée au fond et la pâte se déversait par des conduites en cuivre, puis dans des caniveaux en maçonnerie vers les caisses situées à l’étage au-dessous.
Ces caisses conçues de façon identique à celles sous les défileuses, décrites précédemment, dont le but était d’égoutter la pâte, étaient plus nombreuses pour assurer une réserve importante. Après ce stockage, le produit était chargé dans des hottes en bois placées dans des chariots sur rails et dirigé vers les raffineuses. Après un trajet d’une quarantaine de mètres, le chariot chargé dans un ascenseur hydraulique, était monté jusqu’au niveau des raffineuses. Comme il est indiqué au début de ce témoignage, le chiffon a été remplacé par la pâte de bois et ceci aux environs des années 30. Ce changement a supprimé une grande partie de la main-d’œuvre, la pâte de bois était montée directement aux raffineuses par un ascenseur électrique. Toute la partie haute de l’usine n’était plus utilisée, si ce n’est comme entrepôts. Mais la préparation du chiffon ne s’est arrêtée que progressivement, puisque dans les années 50, il y avait encore 4 à 5 coupeuses-trieuses de chiffon.
Pour l’anecdote, il faut signaler que les salles de triage du chiffon n’étaient pas chauffées. Le chauffage à la vapeur n’a été installé qu’au début de ce siècle. Aussi, les trieuses emportaient avec elles un chauffe-pieds à charbon de bois. Heureusement la mode de l’époque était aux jupes longues, mais cet avantage pouvait avoir un certain inconvénient. Dans tout ce dépôt de chiffons, les souris trouvaient un nid idéal et il n’était pas rare d’en rencontrer ; elles faisaient parti de l’environnement.
Occupée tout à son travail, une trieuse sentit soudain une souris lui monter le long de la jambe, affolée, bloquant la bestiole dans sa progression, elle s’écria en patois « venètz viste los omes » (venez vite les hommes). Que s’est il passé ensuite ? nous n’avons pas de témoignage…
III – LA FABRICATION DU PAPIER
Nous rappelons que ces témoignages recueillis auprès des anciens employés de l’usine, nous permettent de faire revivre un moment l’activité de cette fabrique.
Faisant suite à l’eau et au chiffon, nous vous proposons aujourd’hui la fabrication du papier.
La pâte de bois
C’était la matière première qui a progressivement remplacé le chiffon. Il y avait deux qualités : la pâte dure provenant de Suède, Norvège, Finlande et Canada, qui était fabriquée avec du bois de hêtre ; l’autre qualité, appelée pâte tendre, était achetée dans le Sud-Est de la France. Les essences utilisées étaient le pin et le châtaignier.
Une autre pâte tendre venait de Sorgues dans le Vaucluse et était tirée de l’Alfa qui est une plante d’Algérie.
Acheminées par voie ferrée jusqu’à la gare d’Aouste-sur-Sye, les balles de pâte de bois étaient reprises et transportées par camion automobile jusqu’à l’usine et entreposées au rez-de-chaussée du bâtiment des raffineuses. Ces lots avaient environ 80 cm de haut sur 70 cm de large et pesaient 200 kg, ceci pour les qualités venant de l’étranger et du Sud-Ouest. L’alfa était conditionné en rouleaux de 100 cm de haut et 80 cm de diamètre approximativement.
Du rez-de-chaussée, les balles de pâte de bois étaient chargées dans l’ascenseur électrique et montées au 1er étage où étaient les raffineuses. De là, chargées sur un chariot et conduites devant la raffineuse, l’ouvrier introduisait feuille à feuille la pâte de bois dans la pile. Une particularité : les rouleaux d’alfa devaient être coupés avec une hache au tranchant préalablement mouillé, ceci pour pouvoir plus commodément détacher les feuilles de pâte de bois qui étaient très serrées.
Les raffineuses
Que ce soit de la pâte de chiffon ou de bois, le produit passait obligatoirement dans les « raffineuses ». C’étaient des cuves en maçonnerie ou en béton armé appelées « piles ». Fixée à la base sous le rouleau mobile, se trouvait une platine. Celle-ci pouvait être en bronze munie de crans ou en lave à surface lisse. Celle en bronze était utilisée pour affiner la pâte destinée aux papiers normaux. La pâte était alors travaillée pendant deux heures. Celle en lave était nécessaire pour les papiers très fins (32gr) et le temps de travail était de quatre heures. Il est à noter que la pâte de chiffon avait besoin d’un temps plus long de raffinage (environ 4 heures). Dans la pile, il était ajouté de l’eau et du talc ; ce dernier donnait l’opacité et le poids au papier. Dès que la pâte était prête, elle était devenue très liquide. Une vanne placée au fond de l’appareil permettait au produit de s’écouler vers la pile mélangeuse. Il y avait quatre piles, deux petites et deux grandes. L’équipe de travail se composait d’un responsable, le « Gouverneur et son aide « Le second’. Sur vingt quatre heures, il y avait trois équipes qui effectuaient huit heures de travail. Au-dessous des raffineuses, se trouvait la « pile mélangeuse ». C’était un bassin à trois compartiments hauts et étroits, aux parois lisses avec des retours arrondis, ce qui permettait le glissement de la matière dans la pile. La pâte circulait dans ces compartiments en suivant un parcours sinueux. Le mouvement de la pâte était donné par une pompe. Celle-ci assurait aussi la vidange de la pile. L’équipe des raffineuses ajoutait dans la pâte, de la colle à base de graisses animales (fournies par une tannerie de Romans), et de l’alumine dissoute au préalable dans l’eau. Ces ajouts servaient au collage et au glaçage du papier. Eventuellement, on y ajoutait de la couleur, préparée dans un local au dessus de la pile. Il est à noter qu’il était toujours ajouté du bleu outremer et du rouge rhodamine pour la fabrication du papier blanc. Le temps de mélange de la pâte dans la pile mélangeuse était d’une demi-heure environ. Ce temps passé, l’ouvrier ouvrait la vanne de vidange et la pompe propulsait la pâte vers les trois cuviers de la machine à papier. Au même niveau que la pile mélangeuse était installé « le meuleton ». Cette machine conçue comme les meules à grains, avait deux grandes roues en pierre tournant sur elles-mêmes et simultanément en un mouvement circulaire autour d’un axe en croix. Un socle en pierre avec des rebords en fonte supportait ces meules, dont la fonction était d’écraser les déchets de papier qui venaient de la coupeuse ou de la salle de triage.
Ainsi moulu, le papier était à nouveau mélangé dans les raffineuses, incorporé à la pâte de bois ou de chiffon.
La machine à papier
Les trois cuviers établis en tête de la machine recevaient la pâte qui était brassée continuellement par un grand serpentin hélicoïdal muni de godets en fin de spirale. Ces godets en cuivre se chargeaient de pâte et la déversaient dans le sablier en bois de mélèze qui épurait la pâte. Le mouvement ondulatoire de cet appareil dû à un caillebotis placé dans le fond, conduisait la pâte vers un épurateur qui éliminait les morceaux de produit non dilué, appelé « maton ».
De là, la pâte devenue plus liquide par apport d’eau, avançait sur la table de fabrication : c’était une toile métallique en cuivre supportée par des petits rouleaux ; un mouvement continu faisait avancer le futur papier et simultanément une impulsion latérale lui donnait une oscillation comparable à un tamis, ce qui avait pour effet d’éliminer une bonne partie de l’eau en excès.
Trois caisses d’aspiration de l’eau placées sous la toile métallique venaient compléter le travail de la table de fabrication. Installé à la suite de la toile métallique, le rouleau filigraneur imprimait, dans la pâte essorée, la marque et la qualité du papier.
Ensuite, la presse humide écrasait la pâte, puis les presses coucheuses équipées de feutre commençaient le séchage. Une presse montante faisait grimper le produit qui devenait déjà du papier, vers la sécherie avec ses cinq batteries composées de gros cylindres et de feutres. La vapeur envoyée dans les cylindres séchait le papier. Là se terminait le travail du feutre, mais toujours en continu, le papier s’enroulait dans le cylindre refroidisseur, pour passer ensuite dans les petits cylindres apprêteurs qui satinaient le papier.
Enfin bien visible, il venait s’enrouler sur un cylindre en bois appelé « dévidoir ». Cette bobine de papier avait une largeur de 136 à 152 cm et un poids de 100 à 120 kg.
Les feutres étaient fournis par les Ets Binet à Annonay. Il y avait deux qualités de feutres. Avec les presses coucheuses, c’était un feutre souple et dans la sécherie le feutre était plus rigide. La toile métallique venait de Sélestat dans le Bas-Rhin. Elle était changée de temps en temps, quand son usure était trop importante. Son remplacement était une grosse dépense pour la Papeterie. Aussi, si elle avait un accroc, c’étaient les mains adroites des jeunes femmes qui exécutaient la réparation, comme un stoppage sur une étoffe.
La machine était conduite par le « premier de machine ». Son assistant s’appelait le »second de machine ». Dans cette vaste salle où régnait constamment une chaleur humide, il fallait veiller à obtenir beaucoup de propreté pour éviter que les impuretés viennent tâcher la pâte ou le papier.
Enroulée sur le dévidoir, la bobine de papier était passée à la calandre. Cette opération était réservée au beau papier (registre). La calandre, c’était une machine toute en hauteur, équipée de rouleaux métalliques et en carton durci. Ces rouleaux, mobiles, étaient chargés aux extrémités pour obtenir une pression variable selon la quantité et leur rôle était de satiner le papier. Sortant de la calandre ou directement pris sur la machine papier, les bobines de papier étaient placées sur la coupeuse.
Cette machine pouvait recevoir jusqu’à neuf dévidoirs. Le papier se déroulait, puis était coupé en longueur et en largeur. Cette opération était obtenue avec des guides qui maintenaient le papier en place et des couteaux qui le tranchaient à la dimension désirée. Sans interruption, le papier coupé s’empilait sur des cadres en bois, qui, repris par des chariots, étaient montés au 1er étage à la salle de triage, au moyen d’un ascenseur électrique.
Dans la salle de la calandre, proche de la machine à papier, se trouvait une autre coupeuse, mais celle-ci était réservée aux papiers à filigrane centré. Dans la salle de la machine à papier allaient et venaient le premier de machine et son second, habillés légèrement à cause de la chaleur. Ils surveillaient et corrigeaient éventuellement le fonctionnement de la machine. De temps à autre, le premier de machine contrôlait avec une petite balance le poids du papier, en détachant un échantillon sur le dévidoir. En haut et en tête de la machine, dans un local vitré, le chef de fabrication veillait au bon déroulement du travail. Il préparait les feuilles de fabrication selon les commandes à exécuter. Ces fiches de travail étaient datées, numérotées. Elles indiquaient les qualités et les quantités à introduire dans les raffineuses et dans la pile mélangeuse. Il remettait ces feuilles au gouverneur des raffineuses qui commençait ainsi la fabrication.
La responsabilité du chef de fabrication ne se limitait pas à la journée de huit heures. Il intervenait dès qu’un incident sérieux survenait au cours de la fabrication, que ce soit de jour ou de nuit, puisqu’il y avait trois factions de huit heures. Une parenthèse dans la fabrication du papier : en 1939, pendant les premiers mois du conflit, la Papeterie a travaillé pour l’Armée Française. Elle recevait des ballots de coton-poudre destiné aux explosifs. Comme pour le chiffon, le coton-poudre était lavé, puis défilé et blanchi. Ensuite il était séché dans la machine à papier.
De là, emballé dans les « macules » (papier résistant et épais fabriqué par la Papeterie) il était expédié.
A ce jour, il ne reste qu’un témoin de cette époque ayant participé à ce travail.
Pour le visiteur qui découvrait pour la première fois la machine à papier, ce qui l’étonnait le plus c’était la transformation de cette pâte liquide, qui, après un cheminement compliqué et invisible pour un œil non exercé, arrivait à l’autre bout de cette longue succession d’appareils divers, en papier lisse et brillant…
IV – LA PRODUCTION DE LA VAPEUR
Aussi indispensable que l’eau, la vapeur était l’énergie nécessaire au fonctionnement de la papeterie. Elle était utilisée par la machine à papier, les raffineuses, la colleuse et pour le chauffage des locaux. Autrefois, quand le chiffon était la matière première, elle était employée aux lessiveuses et au chauffage des grandes salles de triage. La chaudière, avec sa grande cheminée de briques rouges, haute de 25 mètres, était installée près de la machine à papier.
C’était une chaudière tubulaire semblable à celle qui équipait les locomotives. Conçue de façon à assurer une production de vapeur importante, sa pression de marche normale était de 5 Kg et même après l’arrêt hebdomadaire, la pression ne descendait guère en dessous de 1 Kg. Le combustible employé jusqu’en 1948 était l’anthracite. Chargé à la pelle dans une brouette, il était déversé dans une trémie où une vis sans fin le conduisait jusqu’au foyer.
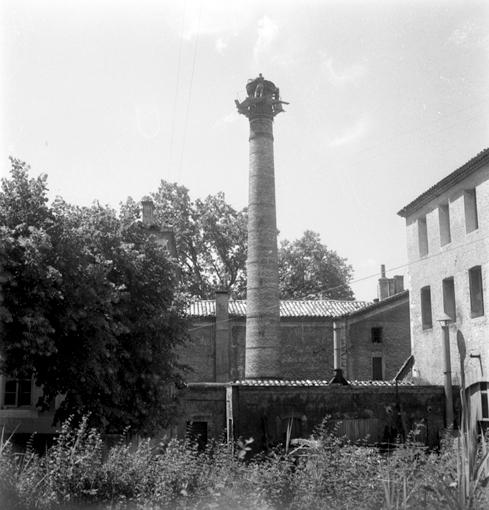
Pendant le conflit de Suez, n’ayant plus d’anthracite, ce sont des briques de charbon qui servaient de combustible et qu’il fallait casser avant de les brûler. Il était à noter que le charbon était toujours légèrement arrosé avant d’être brûlé, ceci pour une meilleure combustion.
De 1942 à 1944, pendant la guerre, n’ayant que des attributions restreintes de charbon, la papeterie a utilisé du bois. Pour cela, quatre bûcherons ont été embauchés. C’était de jeunes hommes qui, refusant le travail obligatoire en Allemagne, s’étaient réfugiés dans la région. Ils étaient originaires de la région lyonnaise. Ces bûcherons abattaient le bois à la hache et le débardaient avec deux paires de bœufs. Ils descendaient le bois jusqu’à un lieu accessible pour le camion à gazogène de l’usine, qui le transportait jusqu’à la papeterie où il était débité. Ces jeunes bûcherons vivaient sur leur lieu de travail et assuraient eux-mêmes leur subsistance. L’exploitation des coupes se situait sur les communes de Soyans, l’Escoulin et Autichamp. Ce travail au grand air était certes très tonique mais pénible ; il fallait assurer 3 à 4 tonnes de bois par jour. Leur salaire était calculé au volume de bois coupé, soit 20 Francs du hêtre, du chêne ou du pin (20 F en 1942 représentent à peu près 26,80 F de nos jours).
La vie de ces jeunes hommes n’était pas sans imprévus, ni incidents plus ou moins drôles, sans oublier leur position de « camouflés » qu’ils devaient toujours garder présente à l’esprit, pour éviter de mauvaises rencontres. Mais à l’écoute de leurs témoignages, on peut penser qu’ils ont quand même de bons souvenirs à évoquer. Le chauffage au bois n’a pas facilité le travail du chauffeur, il fallait charger de façon presque constante le foyer, pour obtenir une pression suffisante, sans oublier qu’il fallait débiter le bois en bûches de 50 cm de longueur.
Un travail pénible et salissant était effectué une fois par an : c’était le nettoyage de la galerie de tirage. Il fallait travailler courbé dans le conduit pour retirer la suie et il va sans dire qu’à la fin de ce travail le chauffeur avait changé de couleur ; plusieurs douches étaient nécessaires pour se débarrasser de la suie, qu’elle soit issue du charbon, du bois ou du fuel.
La chaudière s’éteignait le samedi soir et était rallumée le lundi à quatre heures, ceci pour qu’il y ait suffisamment de vapeur pour la mise en route de la machine à papier à huit heures. Le travail du chauffeur commençait, avant l’allumage, par le nettoyage des tubes de la chaudière et ceci tous les lundis. Ensuite, il surveillait la pression et veillait au bon fonctionnement. Il assurait aussi la surveillance des grilles de la turbine. Pendant la période de fabrication du papier avec le chiffon, le chauffeur surveillait le débit de vapeur aux lessiveuses.
Jusqu’aux environs de 1914, il y avait deux chaudières dont une dans le haut, près du chiffon, mais avec la disparition de cette matière première, seule celle proche de la machine à papier a été conservée. De plus, à côté de celle-ci, se trouvait une petite chaudière de secours ; mais dans les dernières années elle n’a pas été utilisée.
Dans les années 60, une nouvelle chaudière, plus compacte, automatique, semblable à celles utilisées sur les navires (son constructeur était les établissements Babcook-Wilcox), a pris la relève de la vieille chaudière qui devait approcher les cent ans d’âge. Mais les chauffeurs avaient remarqué que dès son extinction, la vapeur tombait à zéro et qu’au bout de quelques années de fonctionnement quelques trous de rouille apparaissaient sur son enveloppe métallique. La fermeture de la Papeterie n’a pas permis de contrôler sa longévité, mais il est à croire qu’elle n’aurait peut-être pas duré cent ans…
Avec le fuel combustible, il avait été installé des conduites d’alimentation en acier. Ces tuyaux partant des citernes de stockage vers la chaudière étaient enterrés dans le sol et passaient sous la galerie de tirage des fumées. L’humidité du sol favorisant la rouille, les conduites de fuel se sont percées et le liquide s’est peu à peu répandu dans le sol, puis dans la galerie de tirage. Ayant constaté cette fuite, la Papeterie avait fait appel à un service de pompage qui devait, dès le lendemain, procéder à l’évacuation de cette matière goudronneuse qu’est le fuel lourd. Mais l’ouverture malencontreuse d’une trappe de visite, ayant provoqué un courant d’air, le fuel s’est enflammé et ce sont des flammes qui sortaient de la grande cheminée au lieu de la légère fumée habituelle. C’était le 14 septembre 1949. Il était impossible de s’approcher de la chaudière. Craignant le pire, la Papeterie a cessé son activité et les bâtiments proches de la chaudière ont été évacués. Plusieurs casernes de pompiers ont été mobilisées, mais ne pouvant rien entreprendre, les pompiers ont surveillé jour et nuit les lieux. Au bout de quarante huit heures, le feu s’est éteint de lui-même et après d’indispensables réparations effectuées avec diligence, l’usine a repris son activité interrompue depuis quinze jours car, sans vapeur, la fabrication du papier était impossible.
La cheminée avait subi un feu trop intense ; il a été nécessaire de la cercler jusqu’à son faîte. Pour cela une entreprise spécialisée est intervenue : l’entreprise Wolfflet de Lyon (qui avait un lien de parenté avec la famille de M. Gustave Odemard). Cette entreprise a échafaudé les 25 mètres de hauteur de la cheminée et a placé des cercles d’acier tout le long du conduit. Les dégâts n’ont été, heureusement, que matériels. La catastrophe a été évitée, car il est probable que le fuel répandu sous les immeubles d’habitation et son embrasement auraient provoqué un sinistre d’une tout autre ampleur.
V – LE SERVICE ENTRETIEN
L’usine employait à plein temps un mécanicien, un menuisier et un maçon.
Le mécanicien avait un atelier équipé d’un tour, d’une raboteuse, de perceuses, de meules, d’une forge et le nécessaire pour la soudure autogène. Cet équipement lui permettait d’intervenir rapidement lors d’une panne. Compte tenu de toutes les pièces mécaniques fonctionnant dans l’usine, sa présence et sa compétence étaient indispensables. Pour le personnel de la Papeterie, son atelier était appelé « la forge », ceci peut-être parce qu’autrefois le travail de forgeron était plus important, en raison de l’assemblage des pièces métalliques obtenu par rivetage. C’est la raison pour laquelle certains forgerons de l’époque étaient nommés « Brûle Fer ».
Le menuisier réparait toute la partie bâtiment : plancher, portes, fenêtres. Cette activité lui permettait de connaître les moindres recoins de ces immenses locaux. Certaines couronnes d’engrenages avaient des dents en bois et c’est lui qui façonnait et remplaçait la denture, en particulier celle du meuleton, assez difficile à exécuter. Il fabriquait pour l’emballage des caisses et des cadres en bois pour l’expédition du papier. Les tabourets des trieuses de papier et autrefois celles du chiffon, étaient aussi de sa fabrication.
Ce travail varié lui permettait de voir travailler tous les postes de l’usine, aussi était-il très renseigné sur la fabrication du papier.
Le maçon était assuré d’avoir de l’occupation, ne serait-ce qu’avec les surfaces importantes de toitures couvertes en tuiles canal. Ce système de couverture avait besoin de temps à autre d’un « remariage ». La réfection des peintures dans les logements du personnel était dans ses attributions. Mais à part ces travaux de routine, il exécutait des ouvrages remarquables en maçonnerie ou béton armé ; la construction des piles des raffineuses en était l’exemple.
Bien sûr, plusieurs générations de ces ouvriers se sont succédées, mais certains, avec une habileté personnelle ou une personnalité particulière, ont marqué leur passage.
Pour les travaux plus importants et plus spécialisés, la Papeterie faisait appel aux entreprises de la région et c’était pour elles un apport d’activité très appréciable. Il était très fréquent de voir « dans les murs » de la Papeterie, telle entreprise d’électricité, de chauffage, de maçonnerie, etc…
La fermeture de la Papeterie, comme beaucoup d’autres établissements au cours des dernières décennies, a certes beaucoup contribué à la disparition dans notre vallée des petites entreprises artisanales, marquant ainsi la fin d’une époque…
VI – LA SALLE DE TRIAGE
C’est la salle où se trouvent actuellement les locaux de la mairie. Les nombreuses fenêtres qui la caractérisent se justifient par le travail qui était réalisé ici.
Les femmes, car c’était uniquement des femmes qui étaient affectées au tri, travaillaient sur des tables, appelées « tôliers », face aux fenêtres : une trieuse par fenêtre. Il y avait cependant une lampe au-dessus de chaque trieuse, que l’on pouvait utiliser par temps sombre. Chaque trieuse avait sa selle à trois pieds pour s’asseoir et un plot pour « se caler » les pieds.
Le papier, coupé à l’étage inférieur, arrivait à la salle par un monte-charge. Le personnel, quant à lui, prenait l’escalier. Le diable avait du mal à sortir si le monte-charge n’était pas à niveau ; celui-ci fonctionnait péniblement avec de lourdes chaînes.
Le matin, deux femmes était désignées pour s’occuper de la roule (ce travail concernait les dernières arrivées à la Papeterie ; il y avait cependant un roulement pour que ce ne soit pas toujours les mêmes). Ce travail consistait à transporter les piles de papier sur un chariot et servir chaque trieuse. Une fois la roule terminée, elles étaient affectées à différentes tâches. Les femmes restaient à la roule tant qu’elles n’avaient pas d’enfants, ensuite elle devenaient trieuses. Les trieuses recevaient donc le papier : la pile emmenée était à droite sur le cadre apporté par le diable. Elles avaient des guides en bois en forme d’équerre (ces guides étaient calés par des plots pour éviter que cela ne bouge), elles remplissaient les guides en fonction de la qualité du papier. Il y avait trois piles de papier : à gauche le papier d’excellente qualité appelé 1er choix ; à droite le papier tâché appelé 2ème choix et le cassé qui était renvoyé au « meuleton » pour une refonte.
Ce papier était trié feuille par feuille pour voir s’il n’y avait pas de défaut ou de pli. Chaque feuille était observée à contre-jour, puis placée dans le guide correspondant. Une autre méthode est apparue dans les années 62/63 : la feuille était glissée, à l’aide d’un doigt en caoutchouc, sans être tournée. Cette méthode était plus rapide mais moins efficace quant à la vérification du papier. Notre compte-rendu n’arrivera certainement pas à traduire toute la dextérité nécessaire à remploi. Nous avons cependant pu admirer l’agileté, l’habilité du geste de certaines ouvrières qui ont bien voulu le faire revivre devant nous car il était plus facile de le voir que de l’expliquer. C’était toute une technique et les femmes allaient très vite dans leurs gestes. Au ralenti on peut vous dire qu’elles ouvraient les feuilles en éventail, elles faisaient ainsi rentrer de l’air pour ne pas casser le papier (c’était le premier geste enseigné). Cela paraît simple quand on le voit mais croyez-le, ce n’est pas facile à faire. En revanche ce geste, une fois acquis, devient un réflexe : même après avoir arrêté leur travail depuis 20 ans, chacune des femmes qui nous a expliqué sa tâche a retrouvé toute sa dextérité. Des femmes spécifiques étaient utilisées : pour 5 fois 5 feuilles comptées, on parlait d’une main. 20 mains étaient égale à une rame, soit 500 feuilles. Chaque rame comportait le numéro de la trieuse qui l’avait exécutée. Il fallait taper le papier pour l’appareiller (le mettre d’aplomb). Le centré était tapé à l’avant des piles. Pour le centré, le rendement n’était pas le même, il était tourné feuille à feuille. Il était tapé et ensuite repris au massicot. Il s’agissait dons le trier, compter et empiler les feuilles. Ce travail était payé à la rame, c’est-à-dire au rendement. Le papier était coupé sous différents formats. Il y avait :
- le coquille (44X56cm),
- le raisin (50X60cm),
- le double raisin (65X100cm),
- le double pot (41X62cm),
- le double tellière (44X64cm),
- le couronne (35X45cm),
- le double couronne (44X70cm)
- le losange pour les enveloppes.
Ces différents formats dépendaient des commandes des clients. Toutes les rames étaient emballées dans un papier appelé « macule », de couleur différente suivant la catégorie, la qualité.
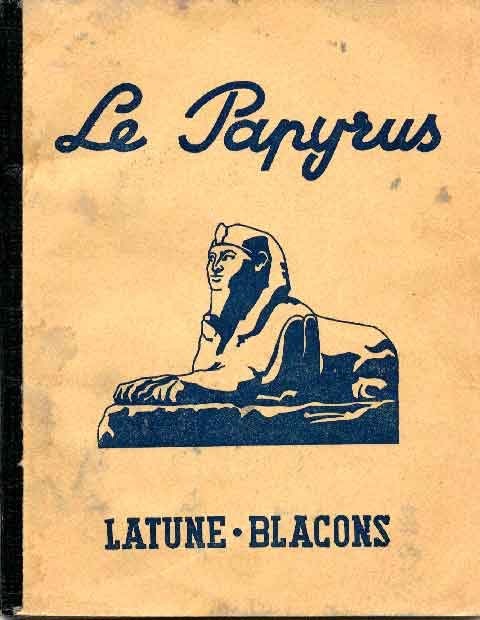
Dans cette grande salle, il y avait aussi d’autres postes :
- au milieu, se trouvait une table servant à envelopper le papier,
- le bureau de la contremaîtresse, laquelle faisait en sorte qu’il y ait toujours quelque chose à faire; elle relevait tout ce que les trieuses faisaient, vérifiait le travail, faisait un peu de comptabilité.
- un passage permettait la circulation des chariots.
Vers les fenêtres, côté nord, se trouvaient le massicot, la régleuse et quelques trieuses. La Papeterie proposait divers articles. Il y avait entre autres : les blocs, les aviblocs, les cahiers, les buvards, les bristols, les cartes de visite, les cartes de deuil, les pochettes dessins…
En ce qui concerne les blocs, il y avait de l’uni, du travers et du rayé commercial. Pour les réaliser, on préparait des rames dans lesquelles était intercalé un carton toutes les 100 feuilles. La rame passait au massicot pour être coupée en 4 ou en 8 (in-quatro ou in-octavo). Une fois coupé, le côté bien lisse était mis au bord de la table, un zinc était posé sur la première feuille pour la protéger ; le bloc pouvait être collé. C’était un travail délicat, qui demandait beaucoup d’attention. Les « roules » préparaient la colle : elles faisaient chauffer de l’eau, y mettraient des tablettes (plus tard des perles) et remuaient pour obtenir une pâte ni trop épaisse, ni trop liquide, sans grumeau. On la préparait dans des bacholes en cuivre, chauffées au bain-marie sur des réchauds électriques. C’était un travail d’équipe car, pendant que certaines fabriquaient la colle, d’autres préparaient les blocs. La couverture et le buvard étaient pliés, on ajoutait une feuille avec ligne pour les blocs unis, la bande encollée sur à peine 1,5 cm de large tenait les feuilles.
Les couvertures et les buvards pliés étaient alignés par 10 et encollés. Seuls, les « grands doigts » pouvaient coller car il fallait tenir la longueur bloc tête-bêche pour que la colle sèche jusqu’au lendemain. Ensuite on les rognait à nouveau au massicot pour qu’ils soient nets.
Les aviblocs étaient du papier à lettre pour l’envoi par avion, fabriqués pendant la guerre d’Indochine. Ils étaient présentés sous forme d’enveloppes contenant 25 feuilles de papier azuré, 25 enveloppes, un buvard et un papier rayé. Au dos de la pochette on pouvait lire : « 1 feuille + 1 enveloppe pèsent moins de 5 grammes ; 3 feuilles + 1 enveloppe pèsent moins de 10 grammes. »
Pour l’emballage, on les mettait dans des caisses en bois. On utilisait la trieuse pour tous les papiers rayés ou quadrillés. Pour les cahiers, c’était la réglure « Sieyès ». Ils étaient formés de 25 feuilles pliées nettes à l’équerre avec la pierre en buis. Ils étaient cousus main. On y mettait également une bande en simili pour tenir le cahier.
Le laminoir
Ce poste de travail se trouvait également dans la salle de triage : il était destiné à satiner le papier bristol. Le travail s’effectuait en équipes. 4 personnes y étaient affectées et elles se relayaient car la tâche était pénible. La machine en elle-même se composait de deux rouleaux qui tournaient en sens contraire ; la pression hydraulique était réglée selon le glaçage désiré (il y avait également une rondelle en fonte qui servait de témoin). Le papier, une fois dans la machine, avançait et reculait deux ou trois fois, selon le glaçage souhaité. Il s’agissait d’enfiler le papier dans le laminoir et ceci se faisait par paquet de 50 feuilles (il était constitué de 25 feuilles bristol et 26 feuilles de zinc). On devait intercaler une feuille de bristol entre deux feuilles de zinc. Ce travail nécessitait une bonne synchronisation : une personne, protégée d’un tablier en feutre, enfilait le paquet qui mesurait environ 2 cm d’épaisseur, dans le laminoir. Il fallait lâcher le paquet dès qu’il était engagé car cela pouvait être dangereux (2 accidents s’y sont produits). Une autre personne sortait le papier satiné de la machine. Deux autres personnes préparaient les paquets sur la table : l’une mettait les nouvelles feuilles et l’autre tournait les zincs. Enfin de journée, il fallait nettoyer les rouleaux car les zincs étaient salissants.
Les cartes de visite
La colleuse servait à coller 2, 3 ou 4 feuilles de bristol ensemble, pour fabriquer les cartes de visite.
Cette colleuse était composée de 2 cylindres dont l’un passait dans une bachole en cuivre contenant la colle. Les 2 cylindres, tournant l’un contre l’autre, s’encollaient mutuellement. Une ouvrière de la roule surveillait le niveau de colle dans la bachole.
Les feuilles de bristol passées entre les cylindres, étaient récupérées par 2 ouvrières qui reformait le paquet (de 250) feuille par feuille en égalisant et en faisant sortir l’excès de colle. Un seau d’eau chaude, à proximité, permettait de se rincer les doigts. Les paquets étaient mis sous presse, de façon que la force soit répartie régulièrement faisant sortir la colle superflue qui était alors éliminée.
Sortis de la presse, les paquets étaient posés sur un chariot roulant puis étendus entre des petites pinces de bois par petits paquets, pour sécher, soit au même étage (étendage fixe), soit à l’étage supérieur (étendage mobile). Une fois secs, les paquets étaient ramassés, retournés, tapés pour être égalisés du côté des pinces, lequel côté était ensuite rogné.
La colle était préparée au « techou ». « Benons » et chaudron servaient à la réaliser. 5 à 6 « benons » de 50 litres de colle étaient faits pour la journée. La recette : 1,2 kg d’amidon, dilué dans un seau d’eau froide, était mélangé dans le « benon » avec de l’eau bouillante stockée dans le chaudron en cuivre alimenté par un jet de vapeur venant de la chaudière à l’étage inférieur. Cette colle était tamisée pour enlever les grumeaux. Les benons vides étaient nettoyés au fur et à mesure. La colle n’était préparée que selon les besoins. Ce n’était pas une activité permanente.
Les carte
s de deuil
Elles étaient réalisées par la même personne. En fin de carrière, une nouvelle personne prenait le relais. Fabriquées à partir des cartes de visites, les cartes de deuil étaient disposées sur une planche avec des clous servant de guides pour les positionner en les espaçant les unes des autres afin de donner l’épaisseur du trait noir.
Les clients choisissaient leur deuil : pour les grands deuils, ce trait était de 7 mm ; pour les petits deuils ou le zéro millimètre, il n’y avait pas de clou mais les cartes étaient disposées très habilement en éventail serré (180 cartes à la fois). Une formule secrète permettait de préparer la pâte ayant l’aspect du cirage pour la consistance.
A l’aide d’un pinceau, cette pâte était déposée en plusieurs sens successifs pour être nette. Ensuite venait l’étape de la brillance du trait, à la brosse.
Les cartes de deuil étaient proposées en plusieurs dimensions de 43 x 83 mm jusqu’à 80 x 120 mm. Les enveloppes étaient faites à Annonay.
Pour donner une conclusion à notre témoignage et en traduire l’impression perçue au cours de notre entretien avec les anciennes ouvrières, nous retiendrons la force du geste de la trieuse, revenue spontanément en démonstration, car plus facile à montrer qu’à expliquer. Pour le visiteur qui pénétrait pour la première fois dans cette immense salle, il était frappé par la propreté et le calme (nécessaire au comptage) qui contrastait avec la salle de la machine à papier située au rez-de-chaussée.
VII- SERVICES ADMINISTRATIFS ET EXPEDITIONS
Nous avons pu remarquer lors des précédents témoignages, l’application qu’apportait le personnel dans I’ accomplissement de sa tâche et le plaisir de chacun à travailler cette matière noble qu’est le papier.
Les bureaux, situés à coté de la salle d’emballage, abritaient les services Direction, Commercial, Secrétariat, Facturation et Comptabilité. Chaque matin, le courrier y était dépouillé selon un rituel quotidien bien établi. Le Président Directeur Général prenait connaissance de tout le courrier reçu, ce courrier transmis d’abord au Directeur était ensuite tamponné et dispatché dans chaque service par la Secrétaire.
Nous nous pencherons plus spécialement sur le service commercial puisque se trouve bien là la locomotive de l’entreprise.
Ce service reposait principalement sur deux personnes :
- L’un responsable commercial sédentaire, était chargé du bon accomplissement des commandes et assurait la responsabilité du service administratif.
- L’autre responsable commercial sur le terrain couvrait une grande partie de la France ; seulement la région Sud était assurée par un représentant.
Vers les années 60, il y a eu ensuite 4 représentants multi-cartes qui sillonnaient la France.
De plus la papeterie possédait plusieurs dépôts-ventes répartis sur toute la France : Paris, Lyon, Marseille, Bordeaux et Alger. Sur ces dépôts, des expéditions avaient lieu régulièrement, notamment sur Paris où des semis entiers partaient fréquemment. Le personnel qui s’occupait de ces dépôts était rémunéré par un pourcentage sur le chiffre d’affaires réalisé.
Les commandes arrivaient à la papeterie soit par courrier ou téléphone, soit par les représentants ou responsables des dépôts. Toutes ces commandes étaient d’abord inscrites sur « le registre des commandes ».
A partir de ce registre, pour les commandes dites « transformées », des fiches de préparation de commande étaient établies. Ces fiches individuelles pour chacun des articles suivaient la commande lors des différents stades de transformation (régleuse, massicot, cartes, façonnage). Le produit terminé arrivait au service d’expédition où une fiche d’expédition avait été établie au préalable.
Pour les commandes prises sur stock, une fiche de réservation de commande était remplie.
Une fiche d’expédition était alors établie pour chaque client avec la désignation précise des produits et la date de livraison demandée. Cette fiche était alors couchée sur « le livre d’expédition » où chaque balle recevait un numéro de référence composé de deux lettres et d’un chiffre. On retrouve déjà ici la notion de traçabilité des produits. Partant de ce registre, il était établi « les étiquettes d’expédition » reprenant les numéros de référence attribués à chaque balle. Ces étiquettes partaient au service emballage pour l’exécution de l’expédition. Les bordereaux d’expédition et de transport étaient alors établis.
Une balle, ramettes de papier empilées entre deux cadres en bois et cerclées d’un feuillard pesait environ cent kg. Toutes les petites et moyennes commandes partaient en balles ; seules les grosses expéditions, notamment sur les dépôts, étaient chargées en vrac.
Toutes ces fiches d’expédition, où figurait le poids exact expédié à chaque client, revenaient aux bureau pour être couchées sur « un registre de facturation » affecté par représentant ou par dépôt. Ces bons d’expédition étaient chiffrés pour l’établissement des factures.
La facturation se faisait au poids pour les papiers et à l’unité pour les articles de papeterie (blocs, ramettes, cartes de visite). Le prix variait selon le poids expédié. Toutes les livraisons effectuées par les dépôts étaient facturées par la papeterie, excepté celui de Paris, le plus important, qui gérait lui-même ses ventes.
Le chiffre d’affaires se faisait essentiellement en vente directe avec les papetiers imprimeurs, clientèle amie très fidèle. La plupart de cette clientèle se trouvait sur l’hexagone, mais la papeterie exportait également sur la Suisse, l’Asie et l’Afrique Noire. Chaque pays demandait une qualité de papier bien définie. Ainsi, durant la guerre d’Indochine, des pochettes de correspondance fabriquées à base de papier très mince, avaient été expédiées à Saïgon pour le trafic aérien.
Les clients réglaient généralement par traite à 30 ou 60 jours ; quelques exceptions à 90 jours. Ces effets étaient envoyés à leur échéance à la banque à Crest pour encaissement. Les effets impayés étaient rares mais existaient tout de même.
L’expédition
Elle était située au niveau du premier étage à côté des bureaux. Un responsable et son aide assuraient le travail. Le papier venant de la salle de triage ou du magasin était déjà plié par rames de 500 feuilles. Il était transporté par des chariots, puis posé sur des cadres de bois sur lesquels on empilait selon les commandes de 12 à 30 rames de papier.
Cette pile de rames était enveloppée dans du papier épais et résistant appelé « macule » ( fabriqué par I’ usine ) puis serrée avec du feuillard d’acier. Il était prêt à être expédié.
Autrefois, le papier était chargé sur le quai situé en haut de l’usine. Il était transporté par une voiture à cheval, mais depuis 1930 environ, c’ était un transporteur avec un camion automobile qui assurait le transport jusqu’à la gare d’Aouste.
L’usine avait deux chevaux que conduisait un voiturier ; il était responsable des animaux et de son véhicule.
Dans les dernières années, le papier était livré dans la région par la papeterie au moyen d’une fourgonnette. Le papier était alors chargé par rame, sans être mis en piles. Le travail de l’emballage demandait du soin, de l’adresse et de la vigilance pour ne pas faire d’erreur dans la préparation des commandes.
Le responsable ou son aide s’occupait aussi de la cloche qui rythmait les entrées et sorties de l’usine. Les dernières années, elle sonnait à 7 H 55 pour la rentrée, 12 h pour la sortie, puis à nouveau 13 h 25 et 17 h 30. Cette cloche était un repaire ; elle donnait de la vie au village. Son silence depuis 1972 a sûrement laissé beaucoup de nostalgie dans le cœur des anciens ouvriers et des autres…
Nous venons d’évoquer le dernier maillon de la chaîne puisque nous sommes arrivés au moment où le produit quitte la chaîne de fabrication. Les maillons de cette chaîne ont toujours été animés par un même élan général : La qualité.
Cette qualité irréprochable a fait la renommée des papeteries Latune.
Signalons que le Général De Gaulle et le Shah d’Iran étaient utilisateurs du bristol fabriqué par la papeterie.
VIII – LA VIE SOCIALE
Après avoir présenté l’activité de l’entreprise, nous vous relatons aujourd’hui, à partir de quelques exemples, l’esprit social qui y régnait.
Elle était probablement au début du siècle une des rares entreprises industrielles du département à développer une action sociale et, à ce titre, faisait sûrement figure de précurseur.
Mme et M. Charles Latune, les propriétaires, habitaient avec leurs trois enfants « la grande maison » au milieu du parc toujours ouvert, que l’on pouvait traverser librement. Malgré leur position sociale qui leur permettait d’avoir à leur service des gens de maison, ils avaient le souci du bien-être de leur personnel. A ce titre, en voici quelques illustrations :
La petite école
Au début du siècle, les mamans emmenaient avec elles leurs bébés dans les ateliers. Ils étaient couchés dans des berceaux en bois qu’elles balançaient régulièrement du pied, pour endormir les enfants lorsqu’ils pleuraient. Par la suite, lorsque les bambins commençaient à marcher et jusqu’à leur entrée à l’école primaire, ils étaient accueillis pendant les heures de travail des parents dans ce que l’on appellerait aujourd’hui « un jardin d’enfants ».
A Blacons, c’était « la petite école ». Dans la maison, à l’angle de l’actuelle Place de la Mairie, face au jet d’eau de l’époque, une pièce au rez-de-chaussée était réservée aux enfants. Ils étaient gardés par une employée qui les occupait :
tantôt dans la salle avec des jeux ou des activités manuelles dont beaucoup avaient comme support le papier. Comment en ces lieux échapper à ce matériau ! Avec des rognures de différentes couleurs, elle leur faisait faire du pliage ou du tissage.
tantôt sur la terrasse, sous le gros tilleul où était installé un grand bac à sable, ou près du jet d’eau.
Dans la salle, il y avait aussi un bac rempli de sciure humide pour permettre aux enfants de jouer à l’intérieur les jours de pluie. Accroché au mur, chacun avait un petit torchon pour s »essuyer les mains à la fin de l’activité, dans un souci éducatif d’apprentissage de la propreté. Dans un coin, les enfants pouvaient faire la sieste, couchés sur des couvertures ou des « macules ».
Les après-midi de beau temps, après la sieste, la gardienne les emmenait très souvent en promenade, « derrière les murs », lieu abrité et sans danger. Le petit groupe montait par le grand escalier, passait devant la ferme et allait jouer à l’ombre sous le gros saule ou patauger dans le ruisseau, à la plus grande joie des enfants. Chacun emportait avec lui un petit panier contenant le goûter donné par les parents. « La petite école » a été fermée en 1940, suite au décès de la responsable qui ne fut pas remplacée. Par la suite, les jeunes enfants furent acceptés à la salle de triage avec leur mère.
Les fêtes de Noël et de Pâques
Chaque année à l’occasion de la Noël, Mme Latune, marquée par ses origines alsacienne, organisait dans le hall de la « grande maison », pour les enfants du personnel, une après-midi récréative. Quelques temps auparavant, aidée de la gouvernante, elle préparait le spectacle en faisant apprendre aux enfants des saynètes et des chants de circonstance dont le traditionnel « Mon beau sapin ». A cette occasion, elle descendait du grenier des malles pleines de déguisements pour le plus grand plaisir des enfants. Il s’agissait d’une initiative préfigurant les arbres de Noël organisés aujourd’hui par les comités d’entreprise.
A l’occasion de Pâques, Mme Latine faisait cuire des paniers d’œufs qu’elle peignait et décorait avant de les cacher dans le parc. Les enfant étaient ensuite invités à venir les découvrir et déguster les traditionnels Suisses et pantins lors du goûter offert pour la circonstance.
L’éducation des jeunes filles
De temps en temps, Mme Latune accueillait chez elle un petit groupe de jeunes filles, après leur travail à l’usine. Elle leur enseignait quelques principes d’éducation ménagère et familiale. Elles y apprenaient comment faire la cuisine, mettre la table, repasser, coudre, broder…
Les logements
Jusqu’en 1936, la plupart des ouvriers étaient logés gratuitement par l’employeur dans les bâtiments des « casernes » et des « cités ». Les autres bénéficiaient d’une indemnité de logement.
Dans le bâtiment des « casernes », aujourd’hui rénové et rebaptisé « Les Rivières », les appartements étaient petits et exigus pour les familles nombreuses. Aussi, lorsque les enfants devenaient adolescents, la plupart des jeunes allaient dormir au dernier étage où étaient aménagés à cet effet deux dortoirs : celui des filles et celui des garçons.
Les maisonnettes, situées de l’autre côté de la départementale 93, furent construites juste avant 1914, à l’initiative de M.Charles Latune. Il y a sept maisonnettes mitoyennes, doubles, soit 14 logements tous construits sur le même modèle et possédant un petit jardin attenant. A l’époque, elles n’avaient pas l’eau sur l’évier mais étaient alimentées par deux fontaines.
Lorsqu’une famille s’agrandissait et ne pouvait plus loger aux « casernes » par manque de place, elle déménageait aux maisonnettes. A l’inverse, lorsque les enfants devenus grands quittaient le foyer, les parents restés seuls devaient libérer le logement pour laisser la place à une famille nombreuse et se réinstaller dans un appartement « aux casernes ».
Les jardins
Ils étaient situés à la place de l’actuel terrain de sport. Chaque famille bénéficiait gratuitement d’un morceau de terrain d’environ 50m2 sur lequel elle cultivait légumes et fleurs. De chaque côté, il y avait un caniveau qui canalisait l’eau du trop plein des bassins de l’usine. Un système de mini-barrages permettait d’arroser facilement les parcelles. A droite des jardins, séparés par un chemin, se trouvaient « les cabanes » : une bonne vingtaine de petits cabanons alignés en 3 ou 4 rangées le long du bâtiment des charrettes, l’actuelle Salle Polyvalente. Ils étaient construits en planches ou en dur et chacun y remisait ses outils, du bois et même pour certain, quelques animaux : lapins, poules, cochons, chèvres…
Au centre du terrain occupé par les jardins, était aménagé un espace réservé à l’étendage du linge qui était lavé tout prés de là, en contrebas dans un grand bassin appelé « la serve ». On y accédait par un petit sentier creusé de marches d’escalier. Dans la pente toute proche du bassin, étaient aménagéS 2 ou 3 foyers permettant de faire bouillir les lessiveuses.
Logements et jardins constituaient à l’époque pour le personnel, des avantages en natures très importants.
Après 1936, suite au mouvement ouvrier, le logement jusque là gratuit, est devenu payant. Le montant du loyer fixé par l’employeur étant alors retenu sur le salaire.
La coopérative
C’était l’épicerie du personnel. Elle était située à l’emplacement de l’actuel restaurant « Les rivières » et était gérée par 2 ou 3 personnes. Elle a longtemps été tenue par une même famille. Comme dans tout système coopératif, au départ, chaque famille adhérente versait une mise de fonds qui était de l’ordre de 100 F. en 1914, ce qui représenterait actuellement environ 1600 F.
Elle était approvisionnée par divers fournisseurs et l’on y trouvait tous les produits d’épicerie, dont de l’excellent saucisson. Chaque famille possédait deux carnets où étaient notés les achats : l’un pour le magasin et l’autre pour la famille. Le règlement se faisait chaque mois au moment de la paie. Selon le principe coopératif, les achats en nombre permettaient d’obtenir des prix par produits bien inférieurs à ceux du commerce local.
En fin d’année, il y avait une répartition des bénéfices entre les adhérents qui pouvait représenter jusqu’à 13%. Pour certaines familles, les courses de décembre étaient payées intégralement par les ristournes. La coopérative était ouverte tous les soirs pendant deux heures après la fermeture de l’usine. Son fonctionnement s’est arrêté quelques années après la fin de la guerre.
Les loisirs
Dans les années cinquante, fut mise en place une journée annuelle de détente organisée par l’employeur pour tous les membres du personnel et leur famille. Le voyage en car et le repas pris au restaurant étaient offerts. L’après-midi était l’occasion de visiter le site ou de jouer aux boules. Ces journées fort appréciées permettaient très souvent de remplir deux cars. La première eut lieu à la Fontaine du Vaucluse, puis d’autres suivirent à Vernoux, Nyons, le pont de Mane, le lac de Laffrey, de Charavines, Châtillon en Diois…
A cette même époque, les familles qui, l’été, envoyaient leurs enfants en colonies de vacances, bénéficiaient pour cela d’une participation financière de l’employeur. Ces actions étaient une façon de redistribuer au personnel, sous forme d’avantages, une partie des bénéfices.
La santé
Dès 1942, le personnel a adhéré à la société mutualiste « l’Avenir » à Crest. La cotisation individuelle était avancée par l’employeur, puis retenue sur le salaire. Pour ce qui est de l’assurance maladie, les personnes concernées devaient apporter au comptable les feuilles de remboursement des soins avant le mardi midi, pour le départ au courrier du jour. Tous les vendredis matin, un cadre de l’entreprise allait chercher les remboursements en argent liquide à la Caisse de Sécurité Sociale de Crest. Le comptable remboursait alors les intéressés.
Lorsqu’une ouvrière, qui avait un poste particulièrement pénible, à « la roule » ou à la manutention ou au chargement, était enceinte, elle bénéficiait d’un changement de poste et passait au triage.
Totalement indépendante de l’entreprise, a fonctionné jusqu’à la guerre à Plan-de-Baix, une maison d’accueil pour femmes et jeunes filles ayant besoin de repos: C’était « Maison Blanche ». Construite au début du siècle et propriété personnelle de Charles et Aimée Latune, totalement financée, gérée et animée par eux. Certaines ouvrières, pendant leur activité, ont aussi pu bénéficier d’un séjour à Plan-de-Baix.
Nous nous devons aussi de mentionner quelques accidents de travail, dont un mortel, qui sont venus attrister la vie de l’usine.
Fonctionnement et vie de l’entreprise
Le propriétaire n’a pas échappé à l’ampleur du mouvement ouvrier de 1936, qui a marqué cette époque. La plupart des ouvriers se sont mis en grève. L’usine a même du être fermée quelques jours. Tout le personnel a reçu une lettre de licenciement puis a été réintégré, à l’exception de quelques personnes. Ensuite, jusqu’en 1968, il n’y a jamais eu de syndicat constitué dans l’usine.
Dans les années cinquante, tout le personnel recevait une participation aux bénéfices de l’entreprise par le versement d’une prime annuelle en fonction du salaire. Celui-ci était versé en deux fois : un acompte le 15 du mois en cours et le solde au début du mois suivant.
Une catégorie de personnel était payée au rendement. Aussi, afin de ne pas dépasser le revenu nécessaire au maintien des prestations familiales, certaines femmes, au triage, s’arrêtaient de travailler avant la fin du mois. Ce fonctionnement était toléré, malgré les quelques difficultés que cela entraînait dans l’organisation du travail.
Nous terminons là nos témoignages et encore tout imprégnés de ce que nous avons entendu et appris, nous vous proposons cette conclusion :
Ecrire un historique de la Papeterie Latune et recueillir des témoignages auprès de ses anciens ouvriers et employés peut paraître aux yeux de certains futile et sans intérêt. Mais est-ce bien inutile de rappeler aux futures générations ce qu’a été l’œuvre et la peine de leurs aïeux ? Certes, les progrès actuels nous font quelquefois regarder avec un œil quelque peu ironique les méthodes de travail du passé, mais sans eux, qu’aurions-nous réalisé, si nous ne nous étions appuyés sur leurs acquis.
A l’écoute de ces témoignages, nous avons rencontré des hommes et des femmes heureux de nous parler de leur travail qui, assurément, leur rappelait leur jeunesse, mais il y avait aussi une certaine fierté d’avoir participé à l’élaboration d’un produit de qualité.
Bien sûr, il faut reconnaître qu’au fil des décennies et ceci depuis 1805, les propriétaires de la papeterie animés d’un esprit d’entreprise peu commun, assorti d’une grande probité, ont su insuffler à leur personnel le goût du travail bien fait. Mais comme il n’est pas d’entreprise qui ne se soit accomplie par le fait d’un seul homme, c’est le travail ,jour après jour, exécuté scrupuleusement par toute une entreprise, qui a permis à la papeterie, pendant plus de 150 ans, de produire ce papier de qualité connu et apprécié en France et à l’étranger.
Mais la papeterie, c’était aussi une structure faite de travail, de convictions et de coutumes. C’étaient des familles qui, de génération en génération, reprenaient le flambeau et continuaient le travail de leurs aînés. Et, c’est cette structure même qui est à l’origine de l’agglomération blaconnaise.
Ce texte est extrait de la brochure » Papeterie Latune et Cie » éditée en septembre 1996 par la municipalité de Mirabel et Blacons